Medical Devices Leaving Patients At Risk
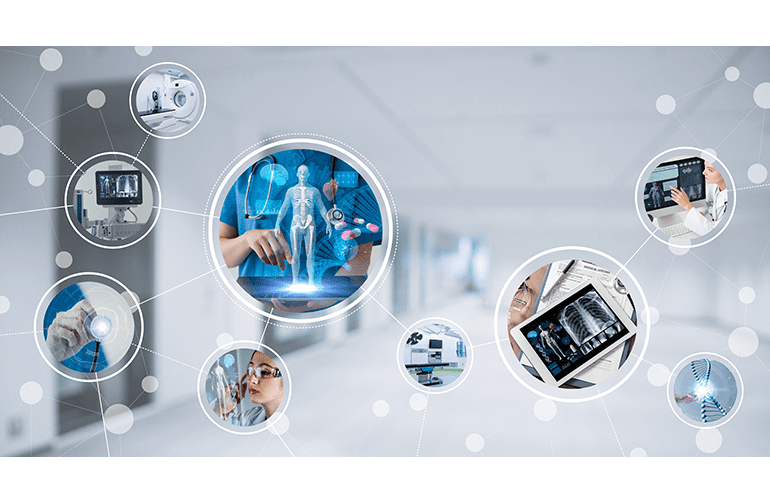
In many healthcare institutions, severe bodily damage and contamination are major issues with medical drugs and devices. Although most issues surface due to faulty device design, issues from Tepezza is one great example of damage caused due to faulty medication. If the procedure for manufacturing the instruments and drugs is well considered and potential reasons are recognized, such issues can be prevented.
This article exclusively discusses several justifications for keeping an eye on medical device corrosion and things to look out for. Together with discussions of the typical origins of instrument issues, problem signs are suggested.
Surgical instruments may become spotty, stained, or corroded, which might affect how well they work. For instance, excessive corrosion can cause tools to shatter during surgery, lead scissors or scalpels to grow dull, and prevent hemostats from opening. Additionally, spots, stains, and rust hinder sterilization. Device life may be limited due to corrosion, which raises the cost of maintenance and repair. Such devices, if used in practice, may lead to illnesses in patients.
Medical tools come in tens of thousands of various varieties. These devices are primarily composed of stainless steel. These devices sometimes have hardened inlays, which can be recognized by their golden handles. The makeup changes depending on the intended use. For instance, a cutting edge will be constructed of soft steel rather than just a grabbing tool. The 300-class stainless steel is generally tougher. The 400 series stainless steel contains the softest steel, like those employed in medical blades. The 300 series’ components are constructed from elements that are more corrosion-resistant.
Stainless Steel
Why is stainless steel used? Hematite, iron, chrome, copper, as well as many other minerals in tiny amounts, make up stainless steel. The quality of stainless steel determines how much of all of these components are used. In principle, a metal’s resistance to corrosion increases with its chromium content. All varieties of stainless steel will corrode and tarnish over time. Additionally, although a device’s exterior may appear shiny and dazzling to the unaided eye, microscopic scrutiny reveals that it is actually very rough. Contaminants from soil and water can be trapped by the hard surface.
The potential of stainless steel to become passivated is among the key characteristics that make it much more resistant to corrosion than carbon steel. The term “less responsive” is more applicable to stainless steel in use in surgical tools. In fact, it is reactive, which means that under specific circumstances, it will rust and discolor. Compared to carbon steel, this discoloration or tarnishing happens far less often. The extra agents that enable passivation do not exist in carbon steel.
The coating of particular metals on the top of stainless steel accounts for the differential in reactivity between that material and carbon steel. The passive layer is the name given to this one. Iron plus chromium oxides make up the majority of the passivation film.
Corrosion, Staining, and Spotting
What do spots, staining, and rusting refer to? On the top of the devices, patches are free or barely clinging to deposits. Usually, they may be removed with a towel and with little friction. If spots are eliminated, instruments are typically not practically or chemically impacted. Spots can be caused by water mineral deposits, vapor residues, and inadequate dirt clearance.
By using deionized or soft water for the last rinse, water crystal staining can be prevented. The creation of mineral deposits during the wash cycle can be prevented by using high-quality cleaning agents. If cleaning agents are not hard-water friendly, they may even contribute to stains. Spots may also appear when cleaning agents are used in excess of the recommended dilution rates. Equipment maintenance is necessary to ensure that the washer receives the proper dosage of cleaning agents.
By maintaining a good steam quality, spotting caused by impurities in the steam can be prevented. This can be accomplished by ensuring that the vapor and boiler water are regularly inspected. Boiler chemicals may leak into the steam generator if the boiler is not properly maintained. Device spotting will result from this. Additionally, any filter and trap connected to water sterilizers need to be cleaned. Furthermore, after making any significant changes to the boiler, the steam pipes need to be cleaned.
Using top-notch cleaning agents will help you avoid spots brought on by inadequate soil removal. Once more, it’s crucial to utilize the right diluting rates and avoid going over what the manufacturer advises. For the first elimination of protein dirt, enzyme presoaks are advised.
Stains, as opposed to patches, are strongly adhering deposits on the top of the device. These spots might be permanently affixed to the surface. But much like with spots, the appearance of stains typically has no physical impact on the devices. Metal replating, polluted steam and several other factors can all result in spots.
Galvanic corrosion is a phenomenon that causes metals to replate. In this scenario, various metals are simultaneously introduced to a fluid. In the liquid, one metal rusts and accumulates on the other. Essentially, a little battery is created. A rainbow-like pattern on a device’s exterior is a sign of the replating. On devices, the stain might also take the form of a golden or rusted hue. By separating different metals and cleaning them at various times, this can be prevented. Separating different metals may not always be possible, though. When that happens, using a safe cleaner for delicate metals can help to lessen the impact.
The soaking time must be minimized to prevent stains brought on by sanitizing solutions. It is not advisable to use disinfectants at higher doses. Additionally, stainless steel devices shouldn’t be employed with iodine preparations.
By maintaining a good steam grade, stains from steam could be prevented, just like stains brought on by steam impurities. Following sterilization, a rainbow- or bluish-colored look on tools is a typical stain. This is often brought on by the steam containing too many neutralizing amines. It really should be mentioned that neutralizing amines are a common occurrence in steam. They are employed to stop the steam lines from corroding. It is possible to avoid using too many neutralizing amines, though.
Conclusion
Medical devices made of corroded and rusted stainless steel have really been linked to infection epidemics. During the sterilization procedure, rusty tools may infect other devices. Recent research has shown that using silicon for medical manufacturing can mitigate several of these issues.
Research Snipers is currently covering all technology news including Google, Apple, Android, Xiaomi, Huawei, Samsung News, and More. Research Snipers has decade of experience in breaking technology news, covering latest trends in tech news, and recent developments.